AAC History
AAC was developed in 1924 by Swedish architect Johan Axel Ericksson and is now being produced in more than 300 factories around the world. AAC is made from fine ground silica sand, Portland cement, lime, water and aluminum powder as an expansion agent. The production process is very carefully monitored to insure a controlled consistency in the proportions and timing of all ingredients that are used in each batch. The materials are first mixed into a slurry and then poured into large molds where the expansion agent reacts with the alkalis in the cement and lime to produce millions of small hydrogen gas bubbles. The mix expands and rises almost 2 times its initial volume. The hydrogen evaporates and the ‘cake’ sets up and hardens into a stable closed cell matrix which can then be precision wire-cut into blocks or panels. The green aerated concrete is then steam cured in a pressurized autoclave for about 12-14 hours where upon it undergoes a second chemical reaction and transforms into the mineral Tobermorite or calcium silicate hydrate. The finished materials are palletized, wrapped and delivered by truck to the job site.
AAC ATTRIBUTES
AAC is lightweight, about a fifth the weight of concrete. (It will float on water).
AAC can be engineered for seismic and hurricane prone regions.
AAC is non-combustible with a UL fire rating of 4 hours for a 4 inch non-load bearing wall. When exposed to fire AAC gives off no toxic gases. Overall, AAC can be a smart material choice for the exterior of a building, given the devastating wild fires recently in the western US.
AAC has unique thermal properties because of its cellular structure. It combines high heat loss resistance for a masonry material along with thermal inertia, resulting in an overall ‘mass enhanced R-value’. AAC is renowned for its energy efficiency in both hot and cold climates, especially in areas that experience large day-night temperature swings.
AAC has high STC ratings and has exceptional sound absorbing characteristics. Because the material has a porous structure containing 70-80% air, it performs as an acoustic insulator to reduce sound transmission.
AAC is impervious to pests, termites and boring insects.
AAC can provide better structural defense in case of storms and flooding. Because it is an inert mineral product, it will not support mold and does not rot or decay.
AAC provides a vapor permeable, breathable wall system.
AAC works a lot like wood. It can be cut, drilled, shaped and sanded with hand or power tools. Electric chases are easily sawn or routed in. One can screw and nail into it and a variety of fasteners are available to meet pull and shear requirements.
The manufacturing of AAC materials is a pollution free process that makes best use of a minimum amount of energy and natural resources.
AAC has been going green for decades and can lead the way to a more sustainable future.
AAC MANUFACTURING PROCESS
BLOCKS
‘Solid’, ‘O’, and ‘U’ Block come in a standard length of 24″, a height of 8″ and will vary in width.
Solid Block is produced in widths of 2″, 4″, 6″ up to 12″.
‘O’ or Core Block comes in 6″, 8″, 10″, & 12″ widths and are drilled out 3″- 4″ in diameter to allow for the placement of vertical re-bar and cement grout.
‘U’ Block come in similar widths and are used to cast reinforced lintels over doors and windows as well as perimeter bond beams.
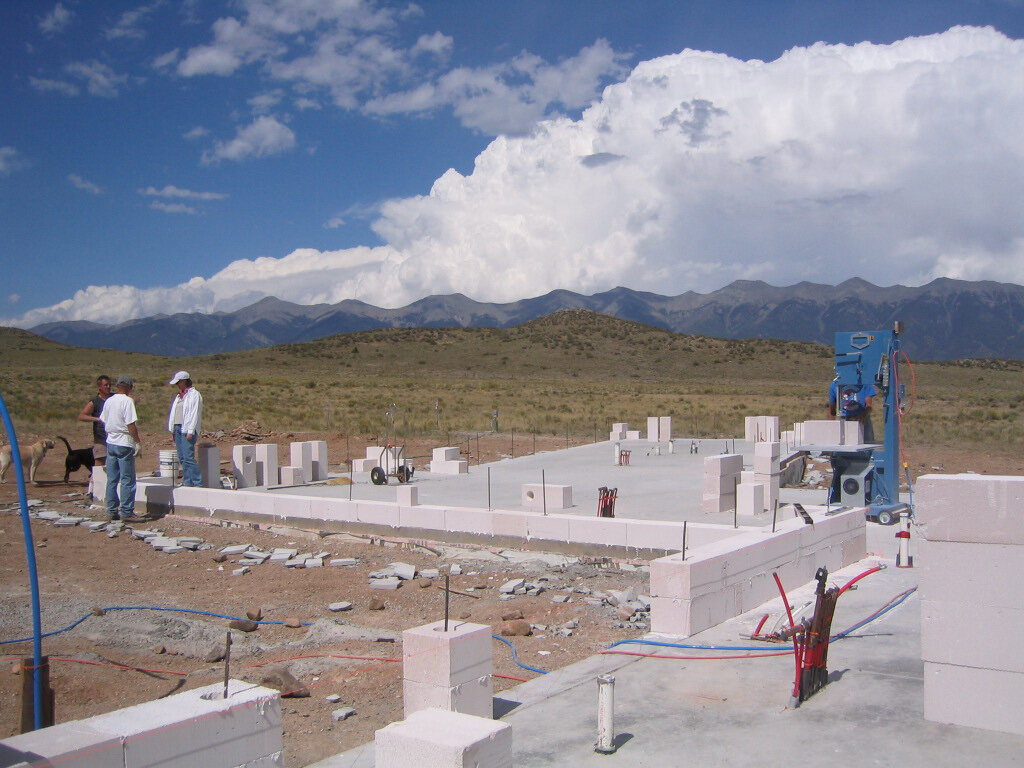
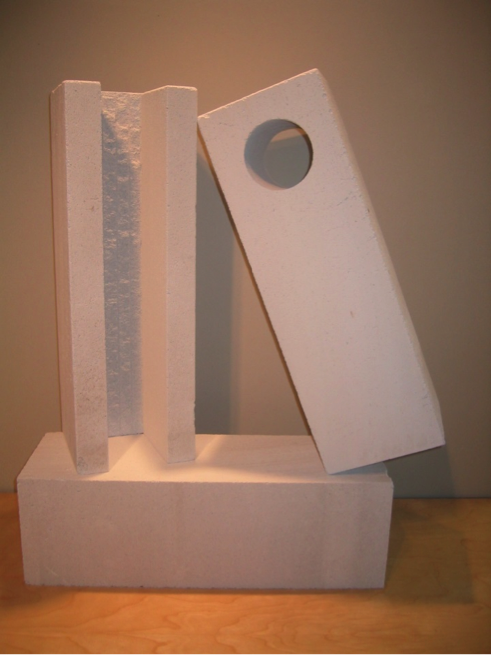
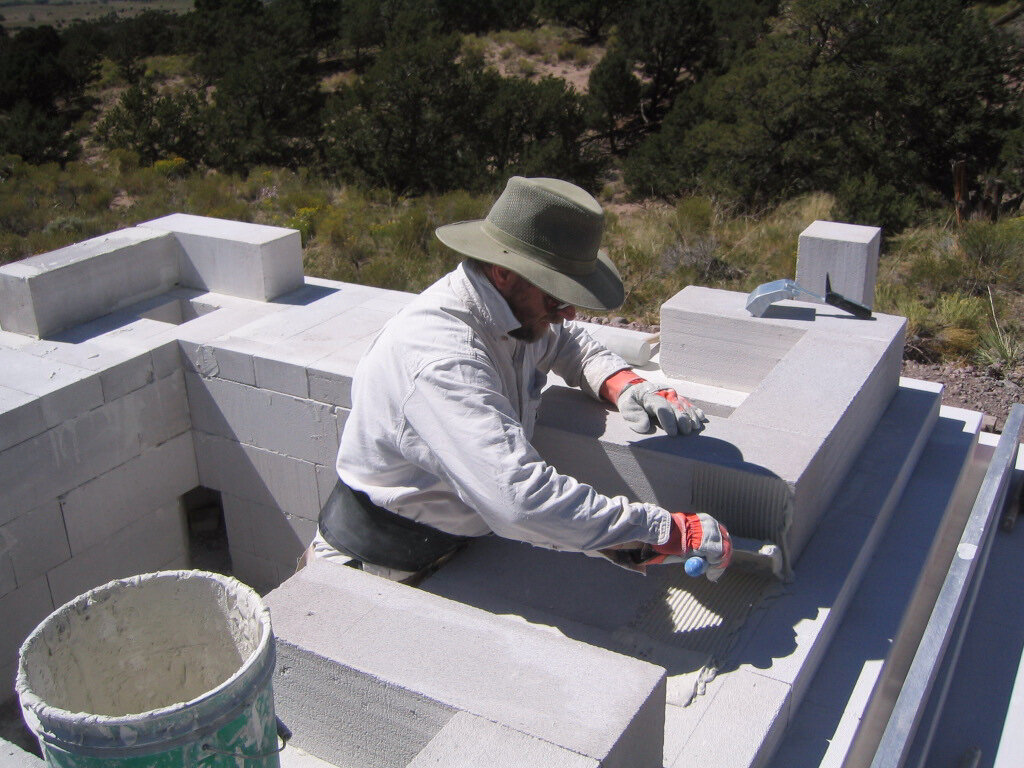
JUMBO BLOCK AND PANEL BOARD
Jumbo Block are manufactured 24″ in height, 32″ – 48″ in length and come in widths of 4″, 6″, 8″ … up to 12″. Panel board can be used for cladding or light structural work and comes in 2’x 4’ by 2”, 3”, & 4” widths.
The larger jumbo block widths require a fork-lift or Mini-crane to lift and place.
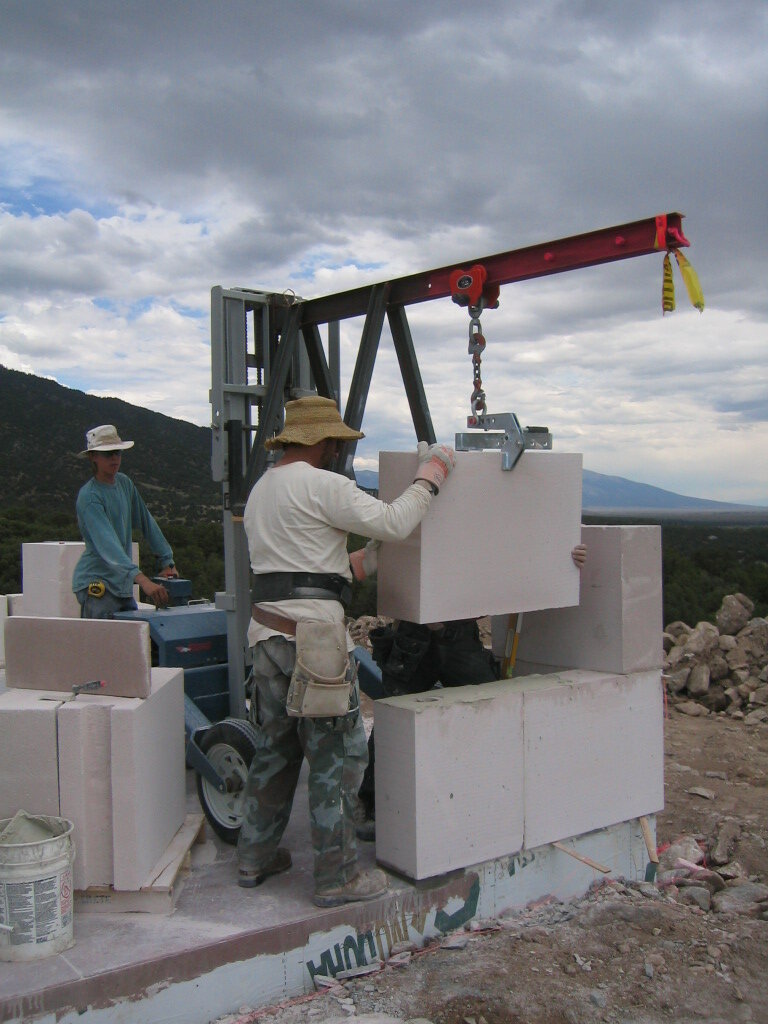
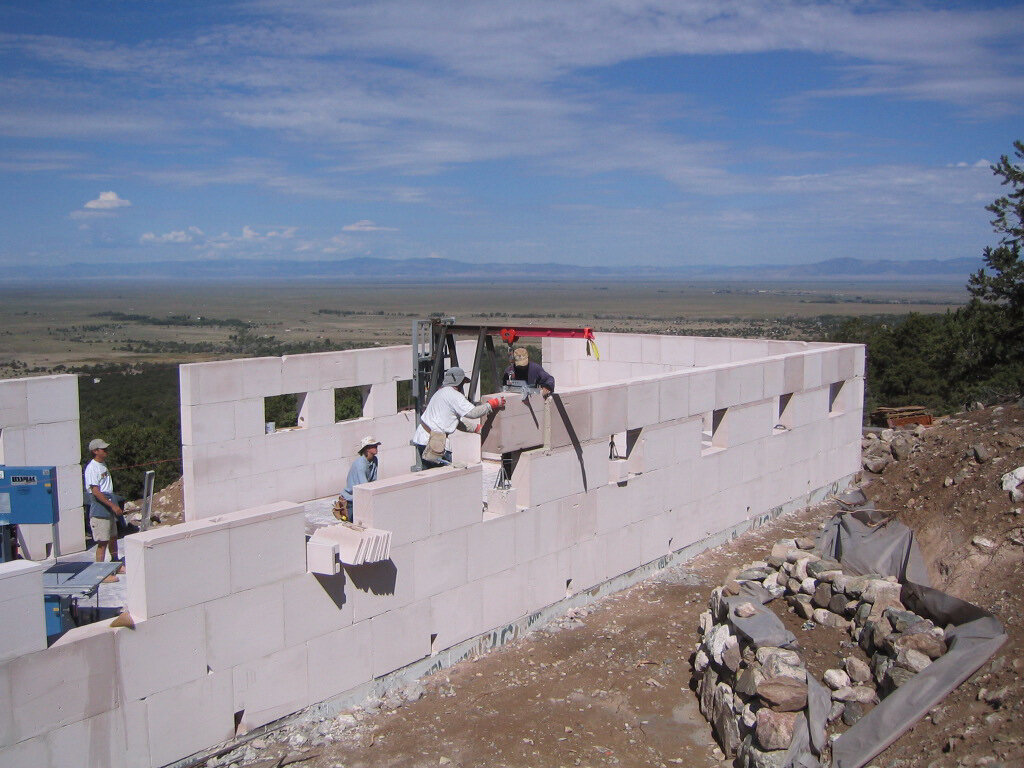
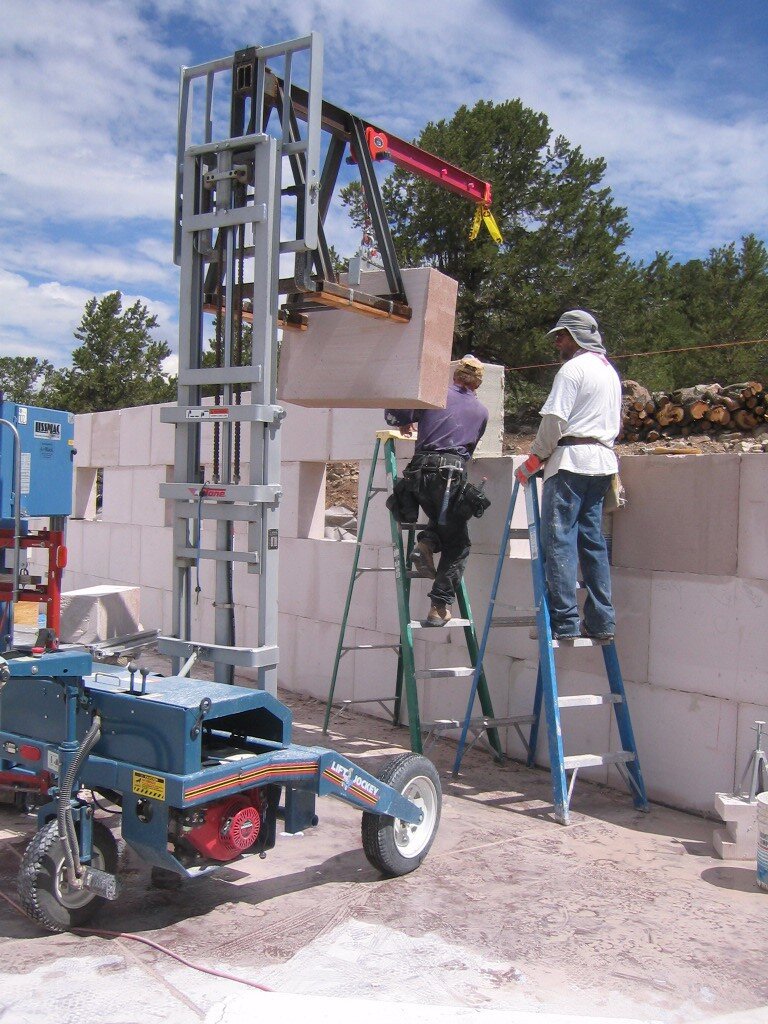
STEEL-REINFORCED PANELS
Panels are a standard 24″ in width, come in nominal thicknesses of 6″, 8″, 10″, & 12″ and up to 20′ in length. They can be used horizontally and vertically for walls, lintels, partitions, floors, roofs and parapets, etc. They are reinforced with embedded welded-wire steel cages and come in an assortment of profiles: Flat to Flat, Flat to C, T&G, and Key Panels. They can be cut to specified lengths at the factory and trucked directly to the building site. Panels are placed in position with jobsite crane and specialized panel clamps.
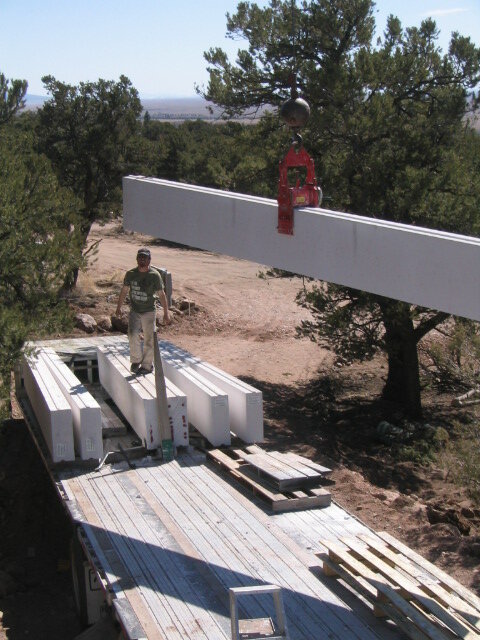
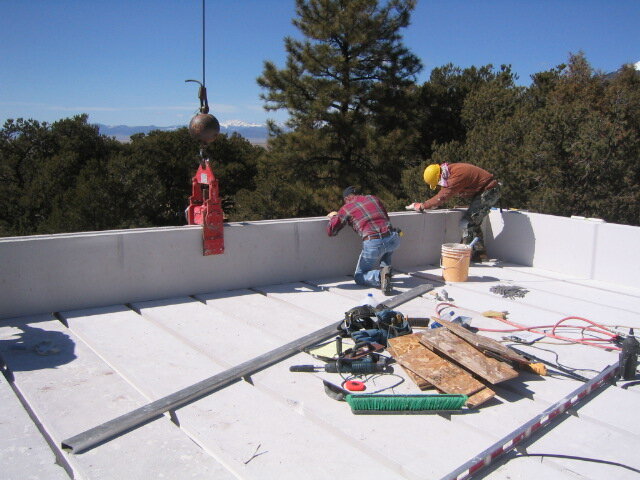
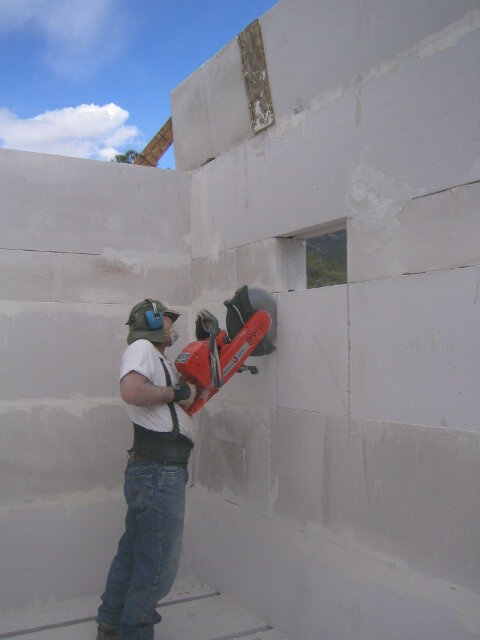
INSTALLATION
Blocks are set on a leveling bed to start the initial coursing. ‘O’ Block is used for steel and grout reinforcement around doors, windows, corners and as specified in the field. AAC can be cut with a carbide hand saw, diamond blade circular saw or AAC band saw. Block is glued together with thin-set mortar using a notch trowel. AAC is easily to drill for cores and lends itself to be worked into a multitude of shapes and designs. ‘U’ Block can be cut to become ‘H’ Block when doubling a lintel or bond beam course. A minimum amount of concrete is required, compared to other block systems, for grouting cores and bond beams.
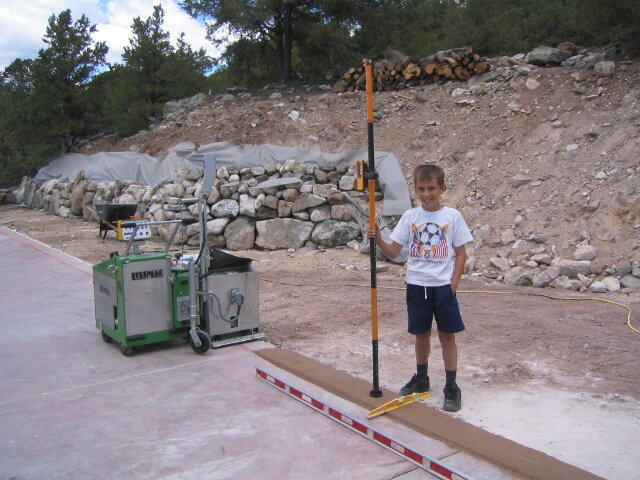

FINISHES
AAC can receive a variety of interior and exterior finishes and coatings. AAC lightweight stuccos are vapor permeable, yet resistant to water penetration. They are applied as a single base coat followed by a color/texture coat. Other exterior materials, for instance, brick, stone veneer, wood cladding, etc., can be anchored to AAC walls. Specialized sand and stone spray finishes have been used for unique surface treatments. For interiors, a number of fine gypsum plaster products are available whose characteristics are compatible with AAC. They are easy to apply as a single hand troweled or spray application. Plasterboard, tile and vapor permeable paints can also be used over AAC. Final veneer coatings can range from structolite and diamond finishes to colored clay paints, adobe & Venetian Marblelino plasters, etc.
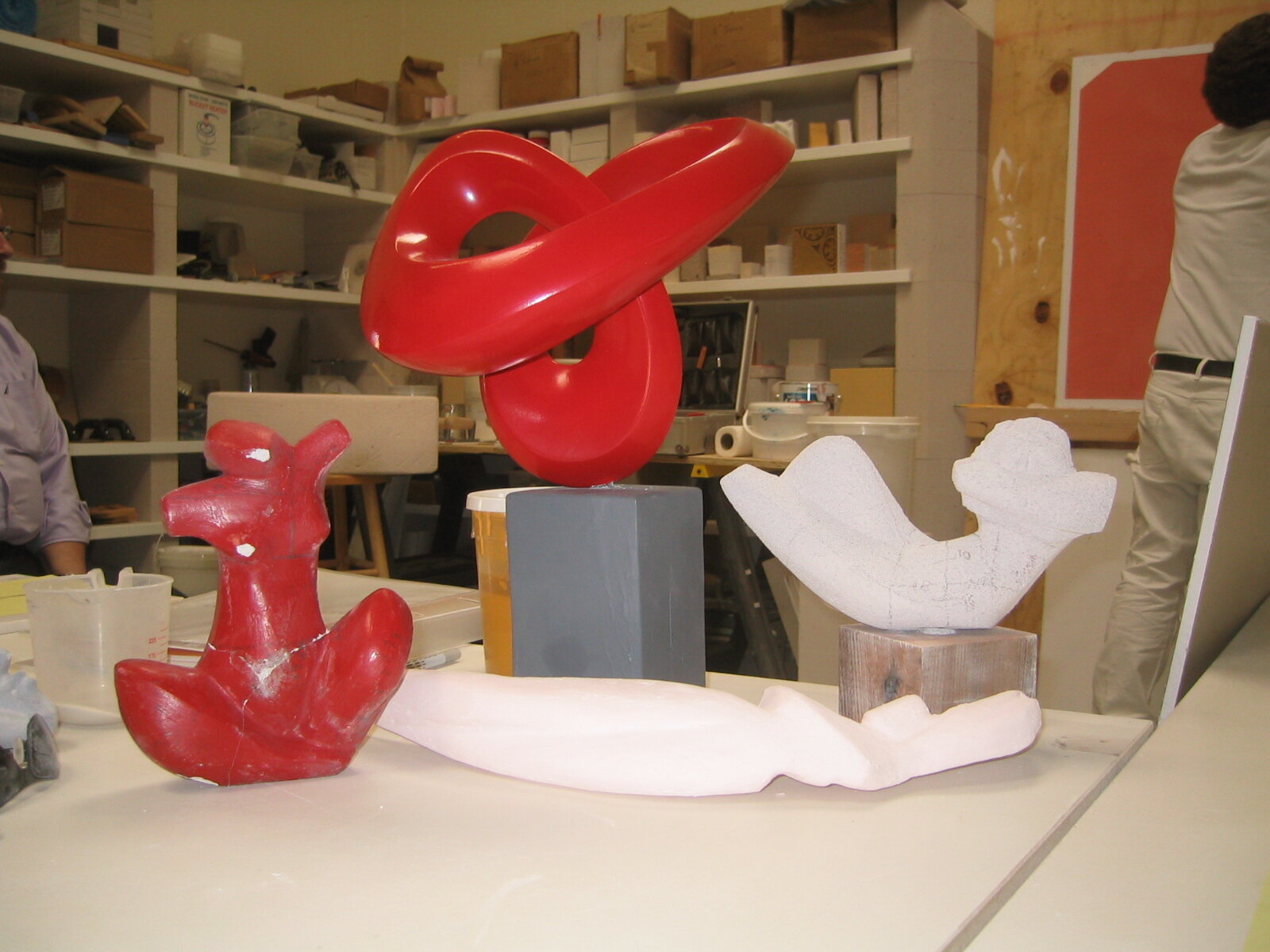
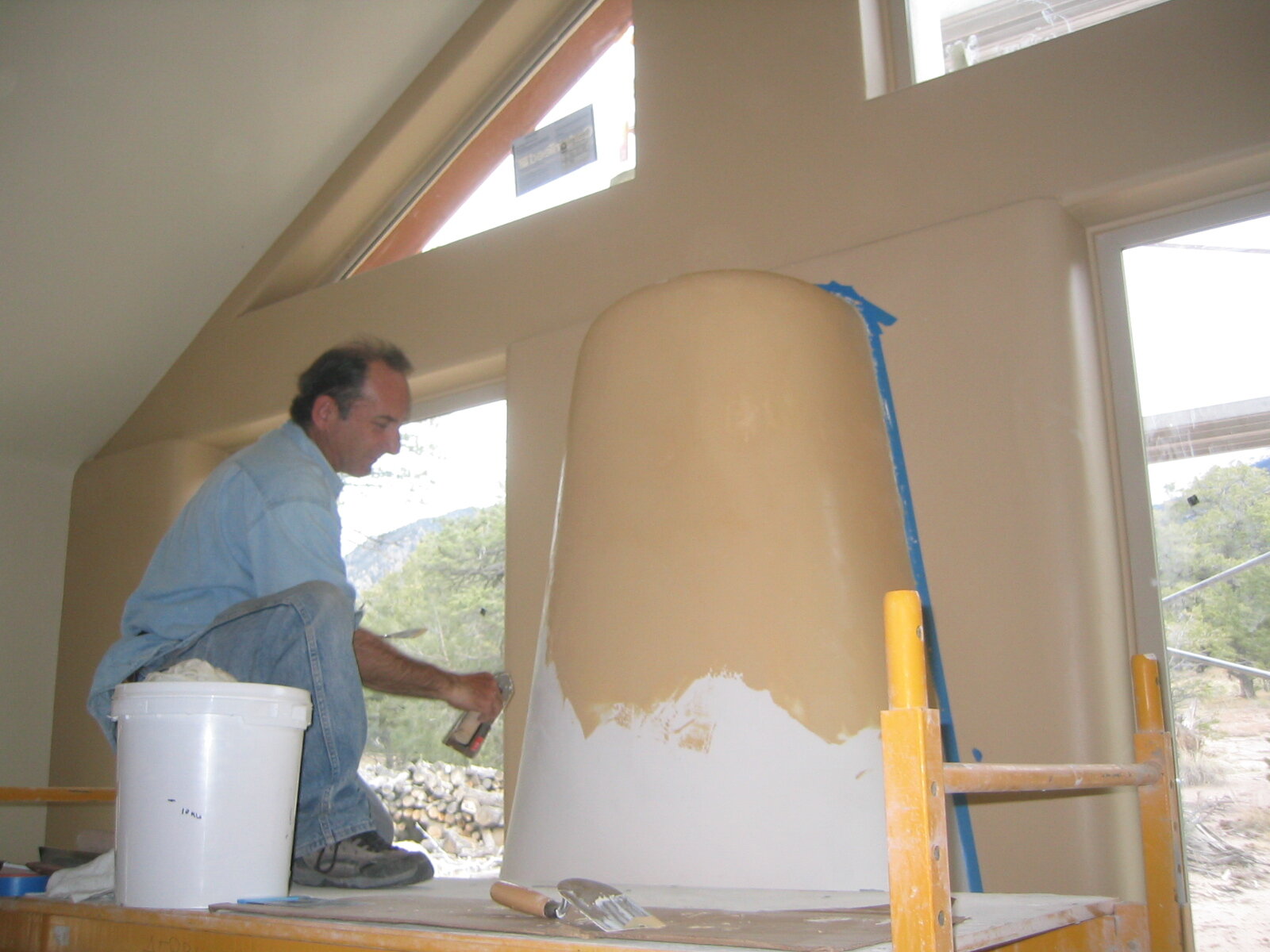
